화학비료라고도 알려진 복합비료는 작물의 영양분 중 질소, 인, 칼륨 중 임의의 2~3가지 영양소를 화학반응 또는 혼합방법에 의해 합성한 비료이다.복합비료는 분말형이거나 과립형일 수 있습니다.복합비료는 유효성분의 함량이 높고, 물에 용해되기 쉽고, 분해가 빠르며, 뿌리에 흡수되기 쉽습니다.그러므로 "속효성 비료"라고 불린다.그 기능은 다양한 생산 조건에서 다양한 영양소의 포괄적인 수요와 균형을 충족시키는 것입니다.
연간 5만톤 복합비료 생산라인은 첨단설비의 조합이다.생산 비용이 비효율적입니다.복합 비료 생산 라인은 다양한 복합 원료의 과립화에 사용될 수 있습니다.마지막으로 실제 수요에 따라 다양한 농도와 배합의 복합비료를 제조할 수 있으며, 작물에 필요한 영양분을 효과적으로 보충하고 작물 수요와 토양 공급 간의 모순을 해결할 수 있습니다.
복합 비료 생산 라인은 주로 질소 칼륨, 과인산 칼륨, 염화 칼륨, 황산 과립, 황산, 질산 암모늄 및 기타 다양한 공식과 같은 다양한 공식의 복합 비료를 생산하는 데 사용됩니다.
비료 생산 라인 장비 전문 제조업체로서 당사는 고객에게 연간 10,000톤에서 연간 200,000톤까지 다양한 생산 능력 요구에 맞는 생산 장비와 가장 적합한 솔루션을 제공합니다.장비의 전체 세트는 작고 합리적이며 과학적이며 안정적인 작동, 우수한 에너지 절약 효과, 낮은 유지 관리 비용 및 편리한 작동을 제공합니다.복합비료(혼합비료) 제조업체에게 가장 이상적인 선택입니다.
복합비료 생산라인은 다양한 작물로부터 고농도, 중농도, 저농도 복합비료를 생산할 수 있습니다.일반적으로 복합비료에는 적어도 2~3가지 영양소(질소, 인, 칼륨)가 함유되어 있습니다.영양성분 함량이 높고 부작용이 적은 것이 특징입니다.복합비료는 균형잡힌 시비에 중요한 역할을 합니다.시비 효율을 향상시킬 수 있을 뿐만 아니라 작물의 안정적이고 높은 수확량을 촉진합니다.
복합 비료 생산 라인의 적용:
1. 유황 함유 요소의 생산 공정.
2. 유기 및 무기 복합 비료의 다양한 생산 공정.
3. 산성비료 공정.
4. 분말 공업용 무기비료 공정.
5. 큰 입자의 요소 생산 공정.
6. 묘목용 모비료의 생산공정.
유기비료 생산에 사용 가능한 원료:
복합 비료 생산 라인의 원료는 일부 점토 및 기타 충전제를 포함하여 요소, 염화 암모늄, 황산 암모늄, 액체 암모니아, 인산 암모늄, 인산 이암모늄, 염화 칼륨, 황산 칼륨입니다.
1) 질소비료 : 염화암모늄, 황산암모늄, 티오암모늄, 요소, 질산칼슘 등
2) 칼륨비료 : 황산칼륨, 풀, 재 등
3) 인 비료 : 과인산 칼슘, 중질 과인산 칼슘, 칼슘 마그네슘 및 인산 비료, 인광석 분말 등
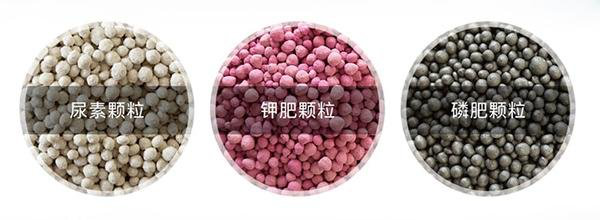
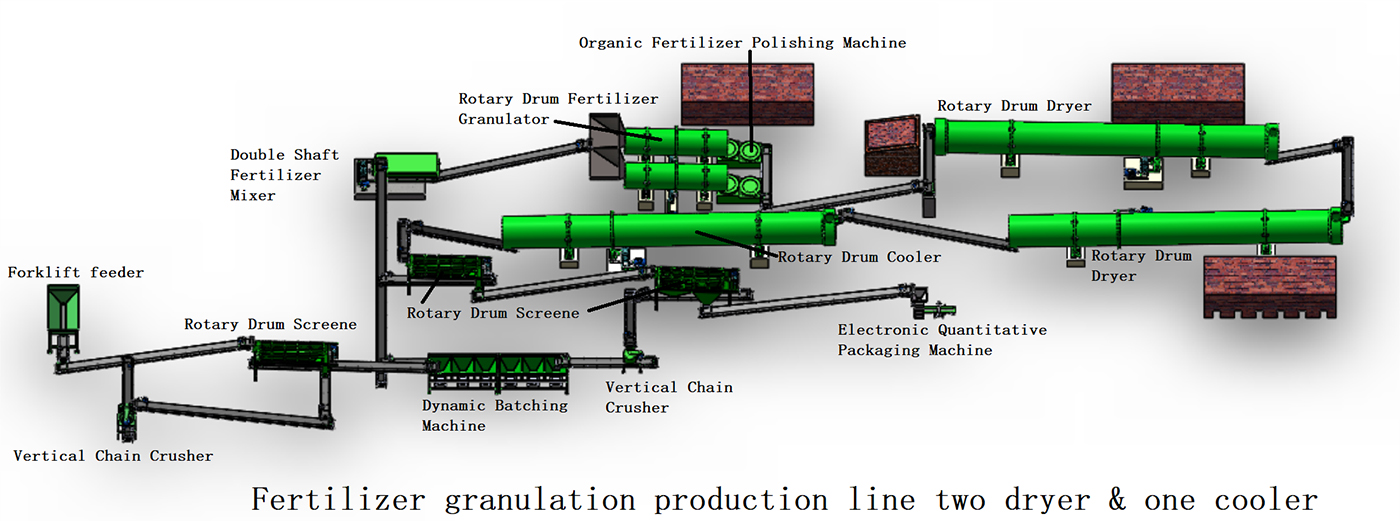
복합 비료 생산 라인 회전 드럼 과립화는 주로 고농도 복합 비료를 생산하는 데 사용됩니다.원형 디스크 과립화는 복합 비료 혼잡 방지 기술, 고질소 복합 비료 생산 기술 등과 결합하여 고농도 및 저농도 복합 비료 기술을 생산하는 데 사용할 수 있습니다.
우리 공장의 복합비료 생산라인은 다음과 같은 특징을 가지고 있습니다.
원자재는 널리 사용됩니다. 복합비료는 복합비료의 다양한 조성과 비율에 따라 생산할 수 있으며 유기 및 무기 복합비료 생산에도 적합합니다.
최소 구형율과 바이오박테리아 수율이 높습니다. 새로운 공정은 90%~95% 이상의 구형율을 달성할 수 있으며, 저온 바람 건조 기술을 통해 미생물 박테리아의 생존율을 90% 이상 달성할 수 있습니다.완성된 제품은 외관이 아름답고 크기도 균일하며, 그 중 90%가 2~4mm 크기의 입자입니다.
노동 과정은 유연합니다. 복합 비료 생산 라인의 과정은 실제 원자재, 배합 및 현장에 따라 조정될 수 있으며 고객의 실제 요구에 따라 맞춤형 과정을 설계할 수 있습니다.
완제품의 영양소 비율은 안정적입니다. 성분의 자동 측정, 다양한 고체, 액체 및 기타 원료의 정확한 측정을 통해 공정 전반에 걸쳐 각 영양소의 안정성과 유효성을 거의 유지합니다.
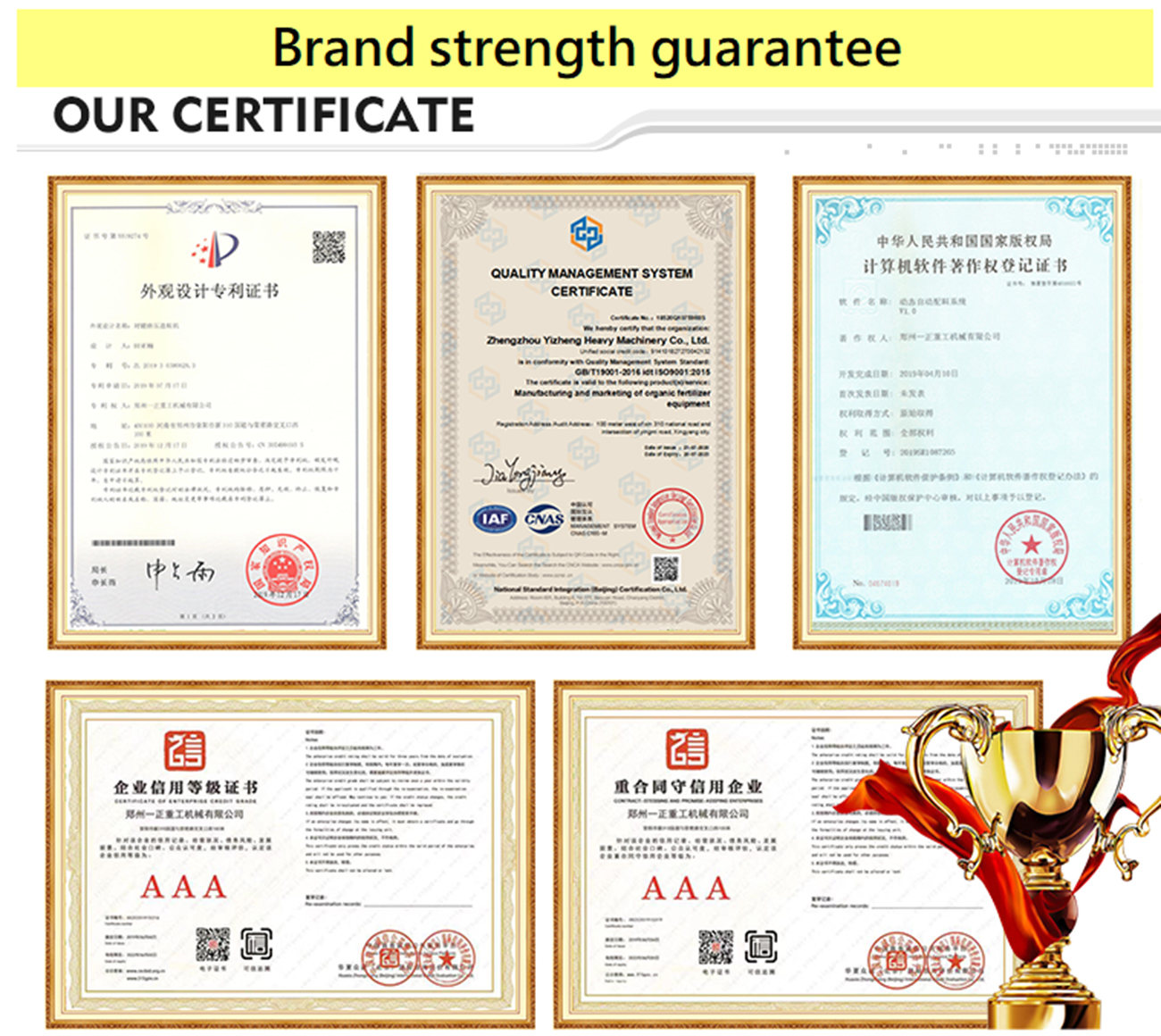
복합 비료 생산 라인의 공정 흐름은 일반적으로 원료 성분, 혼합, 결절 분쇄, 과립화, 초기 스크리닝, 입자 건조, 입자 냉각, 2차 스크리닝, 최종 입자 코팅 및 완제품의 정량 포장으로 나눌 수 있습니다.
1. 원료 성분 :
시장 수요 및 현지 토양 측정 결과에 따라 요소, 질산암모늄, 염화암모늄, 티오인산암모늄, 인산암모늄, 인산이암모늄, 중칼슘, 염화칼륨(황산칼륨) 및 기타 원료가 일정 비율로 분포됩니다.첨가물, 미량원소 등을 벨트스케일을 통해 일정 비율로 성분으로 사용합니다.배합 비율에 따라 모든 원료 성분이 벨트에서 믹서로 고르게 흘러가는 과정을 프리믹스라고 합니다.이는 제제의 정확성을 보장하고 효율적인 연속 성분을 달성합니다.
2. 믹스:
준비된 원료를 충분히 혼합하고 균일하게 교반하여 고효율, 고품질 입상비료의 기반을 마련합니다.균일한 혼합 및 교반을 위해서는 수평형 믹서나 디스크 믹서를 사용할 수 있습니다.
3. 크러쉬:
재료 중의 덩어리를 균일하게 혼합한 후 파쇄하므로 주로 체인 크러셔를 사용하여 후속 과립화 처리에 편리합니다.
4. 과립화:
균일하게 혼합하고 분쇄한 원료는 복합비료 생산라인의 핵심 부품인 벨트컨베이어를 통해 과립기로 이송됩니다.과립기의 선택은 매우 중요합니다.우리 공장은 디스크 과립기, 드럼 과립기, 롤러 압출기 또는 복합 비료 과립기를 생산합니다.
5. 심사:
입자는 체질되고, 자격이 없는 입자는 재처리를 위해 상부 혼합 및 교반 링크로 반환됩니다.일반적으로 롤러 체 기계가 사용됩니다.
6. 포장:
이 공정은 자동 정량 포장기를 채택합니다.기계는 자동 계량기, 컨베이어 시스템, 밀봉기 등으로 구성됩니다. 또한 고객 요구 사항에 따라 호퍼를 구성할 수도 있습니다.유기비료, 복합비료 등 벌크 물질의 정량 포장을 실현할 수 있으며 식품 가공 공장 및 산업 생산 라인에서 널리 사용됩니다.